|
Mercedes Benz Actros 2543
mit Kögel-Kippauflieger im Maßstab 1:24
|
|
|
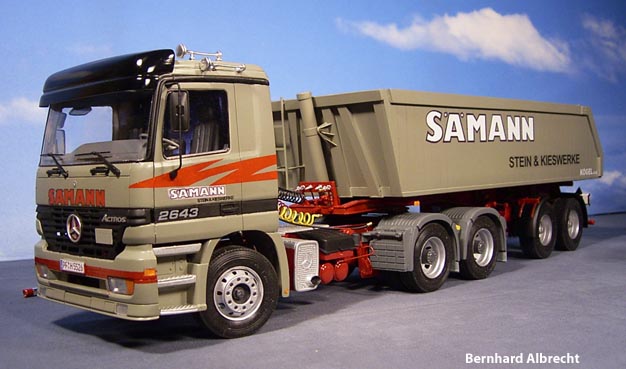 |
|
|
Seit dem Erscheinen des Mercedes Actros bei ITALERI und REVELL, die in
ihren Bausätzen bekanntermaßen die Megaspace-Version (LH) des
Fahrerhauses wiedergeben, habe ich inzwischen auch einige Varianten mit
dem niedrigeren L-Fahrerhaus gebaut. Der Unterschied zum Bausatz lag
hauptsächlich in der Frontschürze, aus der ein Streifen mit den
Zusatzscheinwerfern und Blinkern zu entfernen war. Bei einigermaßen
sorgfältiger Arbeit war diese Änderung ohne Weiteres und mit relativ
geringem Aufwand zu machen. Die Bausatzfahrerhäuser mussten nur
unterhalb der Türen etwas verändert werden. Oberhalb blieb alles beim
Alten, weil alle diese Varianten mit dem unveränderten Hochdach
ausgestattet waren.
Da es mir in erster Linie auf die Realisierung der äußeren Erscheinung
ankam, habe ich auf aufwendige Anpassungen „hinter der Fassade“
weitgehend verzichtet. Deshalb habe ich lieber den Motor durch Weglassen
von Teilen in der Höhe begrenzt, statt den Fußboden bzw. die
Inneneinrichtung anzupassen. Für Modellbauer, die das Fahrerhaus hin und
wieder kippen und daher auf einen detaillierten Motor Wert legen, gäbe
es hier natürlich noch Einiges zu tun.
Die bisher erfolgreich durchgeführten Veränderungen an der
Bausatz-Kabine machten Appetit auf mehr, so dass ich mich schließlich
mit dem Gedanken trug, auch einmal eine dreiachsige Sattelzugmaschine,
möglichst mit dem mittellangen M-Fahrerhaus, zu bauen. Ein passendes
Vorbild hatte ich in Form eines Kippsattelzuges schon fotografiert. Für
die Zugmaschine standen mir einige Zeichnungen zur Verfügung, für den
Auflieger konnte ich jedoch leider keine Unterlagen auftreiben.
|
|
|
Sattelzugmaschine Mercedes Benz Actros 2543 |
|
|
Zuerst versuchte ich, ein vernünftiges
Fahrerhaus
zustande zu bringen, denn damit stand und fiel mein Projekt. Wie beim
Umbau des Megaspace-Fahrerhauses in ein L-Fahrerhaus entfernte ich
zunächst alle Teile unterhalb der Fahrerhaustüren. Durch die
Tieferlegung des Fahrerhauses wanderte der Radausschnitt nach oben, so
dass er noch ca. 4mm in den Wulst unterhalb der Türen reicht. Anhand
einer auf den Maßstab 1:24 umkopierten Fahrerhaus-Zeichnung hatte ich
mir aus Karton eine Schablone des Radauschnitts gemacht, auf die
Seitenwand gelegt und die Konturen mit einem wasserfesten Filzstift
darauf übertragen . Per Feile und Schleifpapier brachte ich den
Radauschnitt in den Seitenwänden ein. |
|
|
Als
Nächstes überlegte ich mir, an welcher Stelle die Sägeschnitte, mit
denen die Seitenwand um 10mm kürzer gemacht werden musste, am Besten
angebracht werden konnten. Wichtig dabei war die Berücksichtigung der
Sicke unterhalb der Seitenfenster, die ja zu allem
Übel schräg nach hinten ansteigt und dann senkrecht
nach oben verläuft. Eine Materialentnahme beispielsweise hinter der Tür,
deren Sägeschnitt weitgehend durch den Türspalt hätte getarnt werden
können, würde unweigerlich zu einem, wenn auch geringen, Höhenversatz in
dieser Sicke führen. So war das also nicht zu machen. Das Ei des
Kolumbus fand ich, indem ich den hinteren Sägeschnitt direkt am Knick
des senkrechten Teils der Sicke anbrachte und den vorderen Sägeschnitt
10mm davor. Auf diese Weise waren nur ein paar Millimeter der
senkrechten Sicke sowie deren Ausrundung in die Schräge nachzuarbeiten,
was mit einer Nadelfeile und Schleifpapier überraschend problemlos
gelang. Diese Arbeiten erledigte ich wegen der besseren Zugänglichkeit
der betroffenen Stelle, bevor die beiden Teile wieder zur kompletten
Seitenwand zusammen gesetzt wurden. |
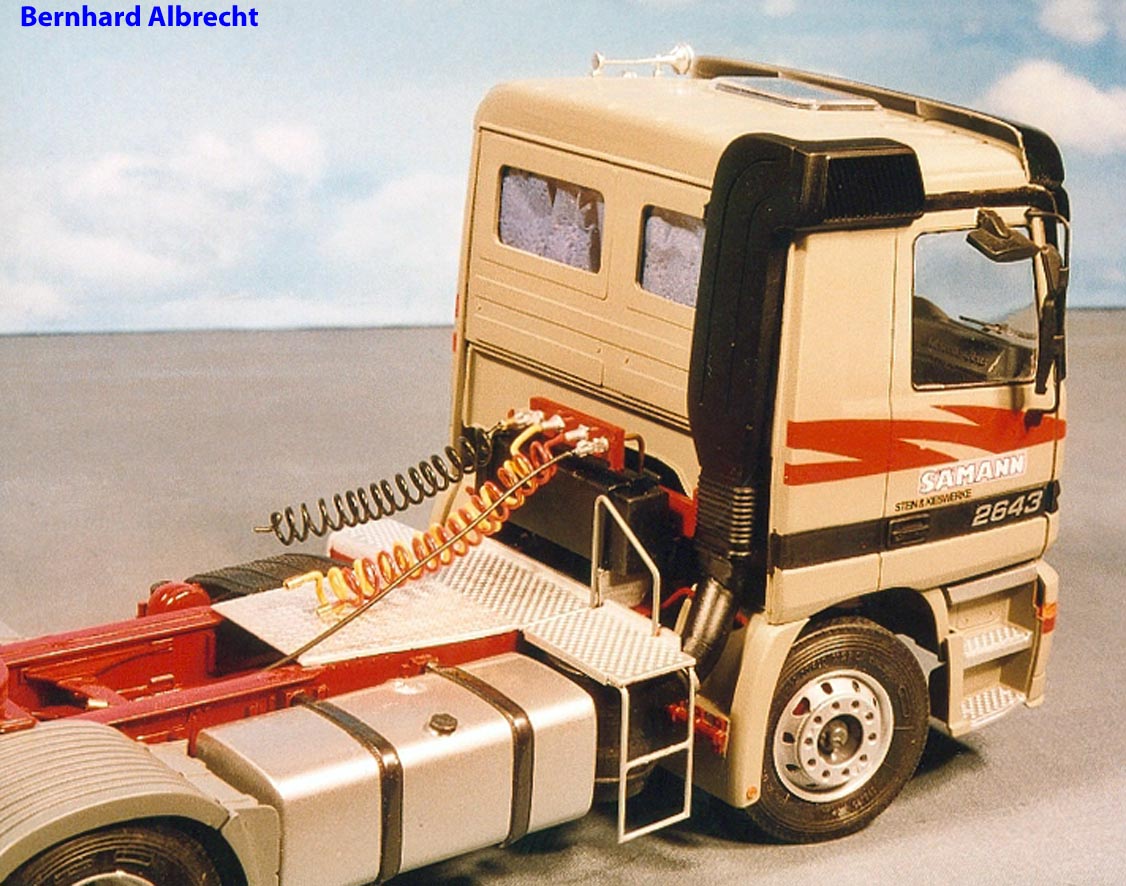 |
|
|
Die
Kabine brauchte in der Breite nicht geändert zu werden, denn zum Glück
ist die Breite der verschiedenen Fahrerhaus-Varianten im Gegensatz zur
Vorgängerbaureihe identisch. Durch den Wegfall des Hochdachs musste ich
allerdings bis auf einen Streifen von ca. 2mm über dem Frontfenster
alles wegnehmen, was zum Dach gehörte. Das abgesägte Teil war jedoch für
eine weitere Verwendung aufzubewahren, da es die Ausrundung zwischen
Fahrerhausfront und Dach beinhaltete. Diese wurde ja auch für das neue
Dach benötigt.
Die Fahrerhausrückseite musste ebenfalls in der Höhe reduziert werden.
Ich habe dazu an passender Stelle einen Streifen von 8 mm oberhalb der
runden Widerlager herausgeschnitten. Die Widerlager wollte ich retten,
damit diese auch beim umgebauten Fahrerhaus ihre ursprüngliche Aufgabe
erfüllen konnten. Den Rest habe ich wieder zusammen gesetzt. Da das
Vorbildfahrzeug auch in der Rückwand Fenster aufwies, habe ich diese an
den bereits vorhandenen Konturen ausgesägt. Bei den Fernverkehrskabinen
sind diese Fensterausschnitte dank des modularen Aufbaus der
Karosserieteile zwar vorhanden, werden jedoch nicht genutzt und sind
deshalb verschlossen.
Aus den bearbeiteten Teilen habe ich nun das Fahrerhaus zusammengebaut.
Um dem Ganzen Stabilität zu verleihen und eine stabilere Basis für das
eigentliche Dach zu haben, habe ich nun eine Art „Innendach“ aus 1m
starkem Polystyrol eingesetzt. Damit die Durchsicht durch die Dachluke
erhalten blieb, habe ich aus diesem „Innendach“ nach dem Aushärten des
Klebers den mittleren Teil wieder ausgesägt. Dadurch blieb im Endeffekt
ein ca. 10mm breiter, im Inneren des Fahrerhauses umlaufender Rand
übrig., der der Struktur des neuen Fahrerhauses eine ausreichende
Stabilität verleiht.
Auf dieses Innendach habe ich nun die in der Höhe gekürzte
Innenverkleidung des Hochdaches mit dem Dachlukenausschnitt gesetzt.
Kleine Unebenheiten wurden mit der Feile egalisiert. Jetzt fehlte nur
noch das eigentliche Dach. Aus dem originalen Dachteil und dessen
Vorderteil, gewonnen aus dem aus der Fahrerhausfront entfernten
Material, habe ich ein neues Dach zusammen gesetzt. Die Länge des Daches
habe ich durch Wegnahme von überschüssigem Material am hinteren Ende
korrigiert. Anschließend wurde die Höhe des Daches durch Sägen und
Schleifen auf ca. 8mm reduziert. Da das ursprüngliche Hochdach nach oben
hin schmäler wird, fehlte nun jedoch etwas in der Breite. Ich behalf mir
mit entsprechenden Kunststoffstreifen von 1mm Dicke, mit denen ich das
neue Dach an den Seiten auffütterte. Das ganze Gebilde wurde nun auf das
Fahrerhaus gesetzt. Dabei musste darauf geachtet werden, dass das neue
Dach vorne bündig mit der Fahrerhausfront verklebt wurde. An den Seiten
und hinten ergab sich ohnehin eine Stufe zu den Seitenwänden. Das
Hilfsdach bot hier eine willkommene Vergrößerung der Klebeflächen. Die
Übergänge zwischen den Seitenteilen und dem Dach mussten nun mit
reichlich Spachtelmasse und dem Einsatz von Feile und Schleifpapier so
lange in Form gebracht werden, bis sie mit den Gegebenheiten auf den
Vorbildfotos übereinstimmten. Der Übergang von der Front zum Dach konnte
mit einer gewissen Gelassenheit betrachtet werden, denn dieser wurde ja
später durch die noch anzubringende Sonnenblende den Blicken entzogen.
Diese Sonnenblende war jedoch wieder ein Kapitel für sich.
Eine weitere Herausforderung war es, einerseits in der rechten, hinteren
Ecke des Daches die Nische für den Kopf des Luftmastes zu schaffen und
andererseits den Kopf des Luftmastes zu ergänzen und in Form zu bringen.
Speziell auf der Rückseite des Ansaugkopfes war viel Material
aufzutragen, denn das Bausatzteil hat ja von Haus aus gar keine
Rückseite, weil diese beim Megaspace-Fahrerhaus ohnehin nicht sichtbar
ist. Hier orientierte ich mich hauptsächlich an den Fotos, nahm Material
weg oder fügte welches hinzu, sowohl am Luftmast als auch am Fahrerhaus,
bis auch hier alles weitgehend mit den Ansichten auf den Fotos
übereinstimmte. Hier war einfach viel Probieren und Vergleichen
angesagt. Aber ich denke, das Ergebnis kann sich sehen lassen.
Als Farbe für das Fahrerhaus habe ich zementgrau (RAL 7033) gewählt.
Diesen Farbton gibt es als Acrylfarbe von Weinert. Hier ist jedoch zu
beachten, dass Weinert Acrylfarben nicht auf Wasser als Lösungsmittel
basieren. Deshalb müssen Polystyrolteile vorher grundiert werden. Ich
verwendete dazu REVELL Airbrush-Grundierung.
Die Form der Sonnenblende war für mich zunächst ein Buch mit sieben
Siegeln, bis ich auf den Trichter kam, eine Sonneblende eines SK zu
nehmen und verkehrt herum auf das Dach zu setzen. Das Ganze etwas
zurecht gestutzt und gefeilt kam in der Form schon ganz gut hin. Den
eigentlichen Blendenteil, der vor der Windschutzscheibe sitzt, habe ich
aus einer Actros-Sonnenblende gewonnen und an die SK-Blende angesetzt.
Diese Komposition wurde mit viel Spachtelmasse in Form gebracht, gefeilt
und geschliffen, schwarz lackiert und an ihrem angestammten Platz
montiert.
|
|
|
Nachdem das Fahrerhaus soweit meinen Vorstellungen entsprach, kam das
Fahrgestell
an
die Reihe. Aus der Zeichnung entnahm ich die Maße des Radstandes
(3300mm/1350mm) und der Rahmenlänge (6865mm), was umgerechnet
13,8cm/5,65cm bzw. 28,6cm bedeuteten. Leider habe ich speziell den
Radstand der Hinterachsen am Modell nicht auch mal mit den Kotflügeln
aus dem Bausatz kontrolliert, denn sonst hätte ich feststellen müssen,
dass die ITALERI-Kotflügel offenbar etwas zu klein im Durchmesser sind.
Deshalb bilden sie nun im korrekt umgerechneten Radstand eine Lücke von
ca. 3mm untereinander, während sie nach dem Vorbildfoto jedoch am
unteren Rand direkt aneinander stoßen müssten. In künftigen Fällen werde
ich diese Lücke durch eine leichte Verkürzung des Hinterachs-Radstandes
verhindern. Die auch am Vorbild an dieser Stelle angebrachten
Unterlegkeile tarnen die etwas zu große Lücke zwischen den Kotflügeln
zum Glück ganz gut weg. |
|
|
Bezüglich der Hinterachsaufhängung gibt es beim Actros zwei Varianten:
zum Einen können die Achsen in einem gemeinsamen Federpaket pendelnd
aufgehängt sein, zum Anderen können sie jeweils einzeln aufgehängt mit
Luftfederung geordert werden. Dankenswerter Weise war das Vorbild mit
den luftgefederten Hinterachsen ausgestattet, so dass ich einfach eine
weitere Hinterachse mitsamt den Montageteilen aus einem zweiten Bausatz
entnehmen und am Rahmen befestigen konnte. Den Durchtrieb von der ersten
zur zweiten Hinterachse stellte ich mit Teilen aus früheren
Mercedes-Dreiachsern von ITALERI dar.
Da bei diesem Vorbild zwei der Luftkessel unter dem Batteriekasten
angebaut waren, habe ich diese statt an den Fahrgestellrahmen an den
Boden des Batteriekastens geklebt. Es waren die Kessel, die aus den
Teilen 97 und 98 sowie 119 und 120 zu fertigen waren. Eine vor dem
Batteriekasten liegende auffällige Leitung habe ich aus Messingdraht
gebogen und eingebaut. |
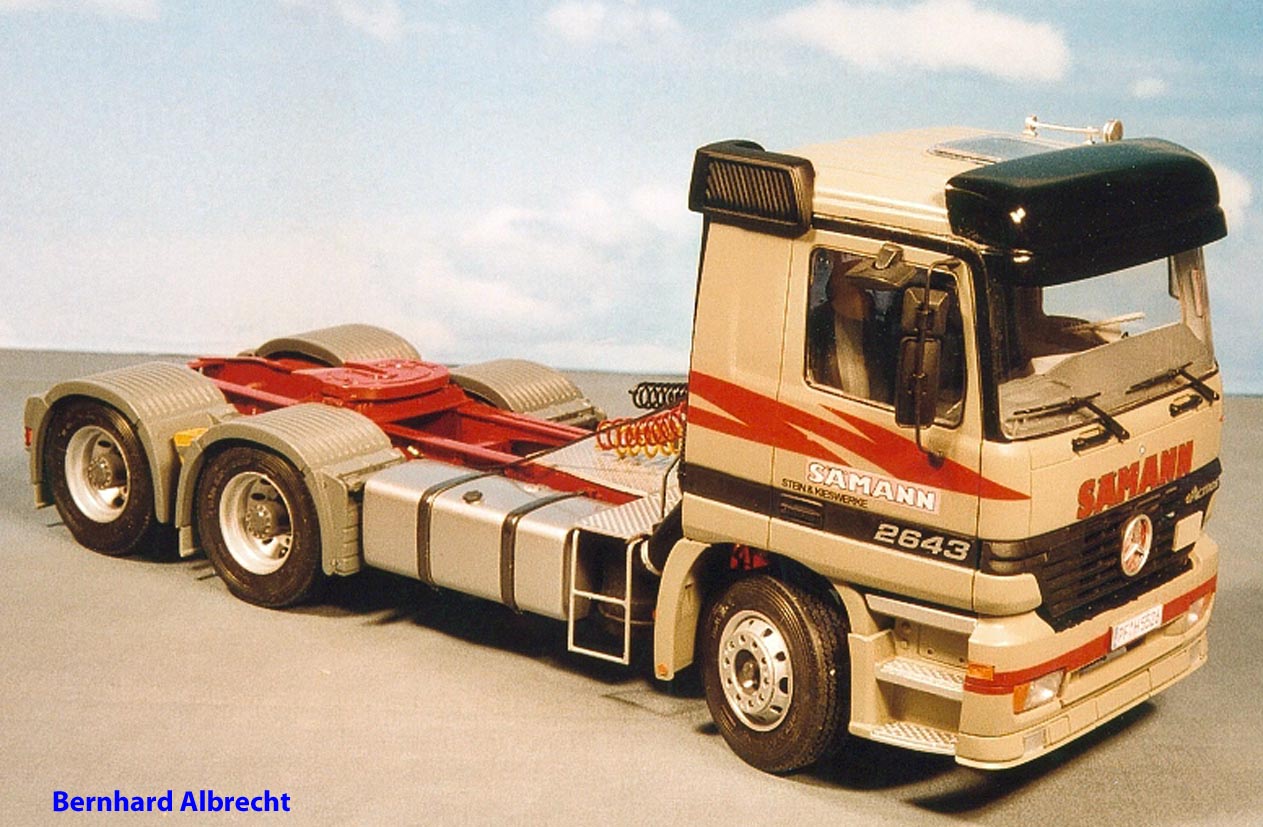 |
|
|
Die komplette Baugruppe war in der
Rahmenfarbe zu lackieren, deshalb habe ich sie gleich fest am Rahmen
angebaut, ebenso den Grundkörper des Auspufftopfs (Teil Nr. 77). Bei
diesem habe ich jedoch vorher noch die Nut verspachtelt, in welche
normalerweise Teil 80 als Auspuffrohr einzukleben ist.
Für die Lackierung des Rahmens habe ich mir aus je einem Teil REVELL 31
(rot glänzend) und REVELL SM 363 (RAL 3004 seidenmatt) eine Farbe
gemischt, die dem Original sehr nahe kommt.
Während die Farbe auf dem frisch lackierten Rahmen trocknete, bereitete
ich in der Zwischenzeit die Anbauaggregate vor. Der Auspuff tritt im
Gegensatz zur Modellausführung aus der seitlichen Blende ins Freie.
Daher habe ich in der Blende rechts unten eine in Fahrtrichtung schräg
nach hinten zeigende Bohrung im Durchmesser von 5mm eingebracht. In
diese wurde ein Kunststoffröhrchen mit dem gleichen Durchmesser
eingeklebt und dessen Austrittsöffnung angeschrägt. Dieses Teil sowie
das Oberteil des Auspufftopfes habe ich in Silber lackiert. In der
gleichen Farbe wurde auch der Tank gespritzt. Diesen habe ich
unverändert wie im Bausatz vorgesehen verwendet. |
|
|
 |
Für die
am Rahmen montierten Teile der Vorderkotflügel konnte ich nichts aus dem
Bausatz verwenden. Diese Teile musste ich völlig neu bauen. Ich habe
dazu Hinterachs-Kotflügel aus älteren Bausätzen genommen und die
Rundung in kochendem Wasser so in Form gebracht, dass sie dem Teil in
der Zeichnung entsprach. Mit einer gemäß Zeichnung aus 1mm Polystyrol
ausgeschnittenen Blende, Evergreen-Profilen und
reichlich Spachtelmasse habe ich versucht, dem
Aussehen des Originals so nahe wie möglich zu kommen. Die Montage am
Rahmen konnte dann mit den im Bausatz vorgesehenen Kotflügelhaltern 76
und 124 erfolgen. Zuvor bekamen sie eine Lackierung in Zementgrau
spendiert.
Ein weiteres Detail, das selbst erstellt werden musste, war der Behälter
für die Hydraulikflüssigkeit. Er wurde aus Polystyrolplatten gebaut und
hat die Abmessungen 14 x 19 x 45mm. Er ruht auf zwei 8mm hohen
U-Profilen und wurde mit zwei Bügeln aus 1mm dickem Messingdraht
fixiert. Auf dem Behälter habe ich auf einer Evergreen-Leiste die Platte
mit den Aufliegeranschlüssen angebracht. Diese stammte aus einem
ITALERI-Zurüstsatz. Auf deren Rückseite habe ich mit Messingdraht die
Weiterführung der entsprechenden Leitungen angedeutet. Sie verschwinden
im Fahrzeugrahmen. Das komplette Bauteil wurde zwischen
Fahrerhausrückwand und Laufsteg (Teil 187) auf den Fahrzeugrahmen
gesetzt. |
|
|
Für
die Komplettierung des Laufsteges mussten noch zwei Bauteile angefertigt
werden. Zum Einen war dies der Handlauf. Das entsprechende Teil des
Bausatzes (Teil Nr. 188) ist leider nicht verwendbar. Aus 1mm dickem
Messingdraht habe ich einen neuen Handlauf gebastelt. Da die
Seitenschürzen nicht angebaut werden, fehlen die Aufstiegstritte zum
Laufsteg auf der Beifahrerseite. Auch diese habe ich aus Messingdraht
zusammen gelötet und am Laufsteg angebracht.
Ein Teil, über dessen Herstellung ich relativ lange gegrübelt habe, ist
die Verbindung zwischen Luftmast und Luftfilterbehälter. Schließlich
schnitzte ich etwas aus dem ähnlichen Teil eines Mercedes SK-Bausatzes,
verlängert mit einem breitgedrückten Plastikrohr und viel Spachtelmasse.
Eine richtig fiese Fummelei, daher kaum erklärbar. Zum Schluss sah es
aber doch ganz passabel aus, wenn auch nicht genau wie am Vorbild.
|
|
|
Der Kippauflieger
Leider standen mir für den Kögel-Auflieger keine Maßzeichnungen zur
Verfügung. Ich behalf mir deshalb damit, ungefähre Abmessungen aus den
Proportionen des kompletten Lastzuges zu errechnen, von dem ich ein Foto
von der Seitenansicht angefertigt hatte. Im Großen und Ganzen stimmte es
mit Abmessungen ähnlicher Fahrzeuge überein. Deshalb beschloß ich, das
Modell nach den errechneten Maßen zu bauen und begann mit dem
Fahrgestell
Für den
Fahrgestellrahmen habe ich eine Länge von 30,6cm ermittelt. Gebaut habe
ich ihn aus Rahmenteilen, wie sie bei den ITALERI-Modellen, des
Lebensmittel-Tankers oder des alten Kühlaufliegers Verwendung fanden.
Das Rahmenvorderteil (d.h.: der niedrigere Bereich des Rahmens um den
Königszapfen herum) war um 3,7cm zu verlängern, das hintere Rahmenteil
jedoch deutlich zu kürzen. Die Rahmenquerverbindungen habe ich
weitgehend nach Stabilitätsgesichtspunkten angebracht, so z.B.
vorzugsweise an den Stellen, an denen auch die Achsaufhängungen am
Rahmen montiert werden sollten. Die Querverbindungen im Bereich der
Achsen habe ich dabei als Kastenträger ausgebildet, indem ich zwei
gleiche Bausatzteile mit der offenen Seite gegeneinander zusammengeklebt
habe. An der letzten Querverbindung habe ich zwei Luftkessel aus dem
gleichen Bausatz angebracht.
|
|
|
Bei
meinem Modell befindet sich der Königszapfen 5,9cm hinter der
Rahmenvorder-kante. Wegen der vorderen Rahmenverlängerung habe ich auch
die Grundplatte mit dem Königszapfen mit Polystyrolplatten nach vorne
verlängert. Ca. 3,6cm hinter der Rahmenvorderkante habe ich an beiden
Seiten mittels kleinen H-Profilen Halter für die Seitenrückstrahler
angebracht. Zwischen Aufliegerstützen und erster Hinterachse wurden die
Bremskeile befestigt.
Das hintere Rahmenende wurde, wie bei Kippern üblich, nach unten
abgeschrägt. Für die Aufnahme der Kippwelle habe ich ein Stück
Messingrohr auf der Schräge befestigt. Hierbei war zu beachten, dass die
Oberkante des Messingröhrchens nicht über die Rahmenoberkante überstehen
durfte, sonst hätte die Kippbrücke nicht richtig auf dem Rahmen
aufliegen können.
Die hintere Querverbindung des Fahrgestellrahmens mit |
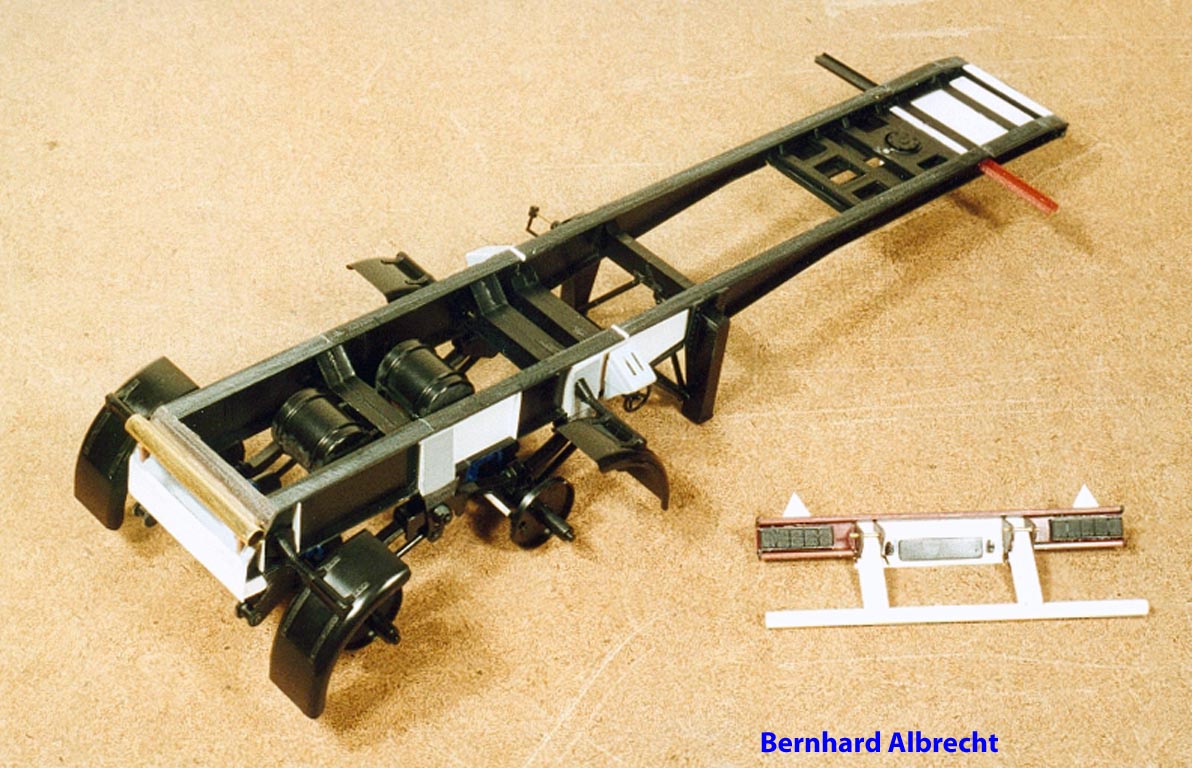 |
|
|
dem
klappbaren Unterfahrschutz habe ich aus Bausatzteilen, Polystyrol
platten und –röhrchen sowie einem ausgedienten Unterfahrschutz aus einem
ITALERI-Bausatz gebastelt. Von diesem habe ich zuerst einmal die
Rücklichter und Nummernschildbeleuchtungen weg gefeilt und geschliffen.
Anschließend wurde der mittlere Bereich des ehemaligen Unterfahrschutzes
ausgesägt, damit er den Rahmenabschluss aus 1mm Polystyrol und die
Nachbildung des Klappmechanismus sowie das Kfz-Nummernschild aufnehmen
konnte.
Die 5-Kammer-Rückleuchten stammen aus einem Zubehörset von Italeri, die
Anhängerdreiecke habe ich aus einer Poystyrolplatte ausgeschnitten und
auf den ehemaligen Unterfahrschutz geklebt. Die Nachbildung der
Nummernschildbeleuchtung erfolgte durch passend gefeilte Stücke eines
Evergreen-Profils. Das ganze Gebilde habe ich dann an das Rahmenende
geklebt.
Die Achsen und Räder stammen aus dem alten ITALERI-Bausatz für einen
Kühlauflieger. Die Position der Achsen habe ich aus einer Seitenaufnahme
des Aufliegers errechnet und angezeichnet. Speziell die Blattfeder für
die hintere Achse musste gekürzt werden, damit sie nicht über das
hintere Rahmenende hinaus ragt, und mit einer selbst gebastelten
Aufhängung am Rahmen befestigt werden. Wenn ich das Fahrgestell noch
einmal bauen müsste, würde ich heute wahrscheinlich lieber einen der
aktuellen Schmitz-Auflieger schlachten und ein luftgefedertes Fahrwerk
einbauen.
Die Aufliegerstützen habe ich lt. Bauplan angebracht, obwohl das Vorbild
keine derartigen Teile aufweist. Wahrscheinlich werden solche Züge im
Betrieb selten getrennt. Die Viertelkotflügel habe ich einem
ITALERI-Zurüstsatz entnommen. Sie entsprechen den Teilen, die auch bei
dem dreiachsigen Pritsche/Plane Auflieger von REVELL enthalten waren.
|
|
|
Kippmulde
Für
die Kippmulde habe ich eine Länge von 21,1cm, eine Höhe von 6,2cm und
eine Breite von 10,1cm ermittelt. Für die Bodenteile der Kippmulde griff
ich auf Bodenteile des Kühlauflieger-Aufbaus von ITALERI zurück. Alles
andere musste im Eigenbau aus Polystyrolplatten und –profilen gebaut
werden. Als erstes fertigte ich mir eine Zeichnung mit der Seitenansicht
der Kippmulde an. Nach dieser schnitt ich die Seitenteile aus einer
1,5mm starken Polystyrolplatte aus. In die ausgeschnittenen Teile ritzte
ich dann Fugen entsprechend den Originalfotos ein. Als nächstes habe ich
aus 2mm dickem Polystyrol mit der Proxxon-Tischkreissäge 7,5mm breite
Streifen ausgesägt, mit denen ich die Verstärkungen an der
Muldenoberkante nachbilden wollte. Diese habe ich dann auf die
Seitenteile oben und hinten angeklebt. An den abgewinkelten Stellen war
auf entsprechende Gehrung zu achten. |
|
|
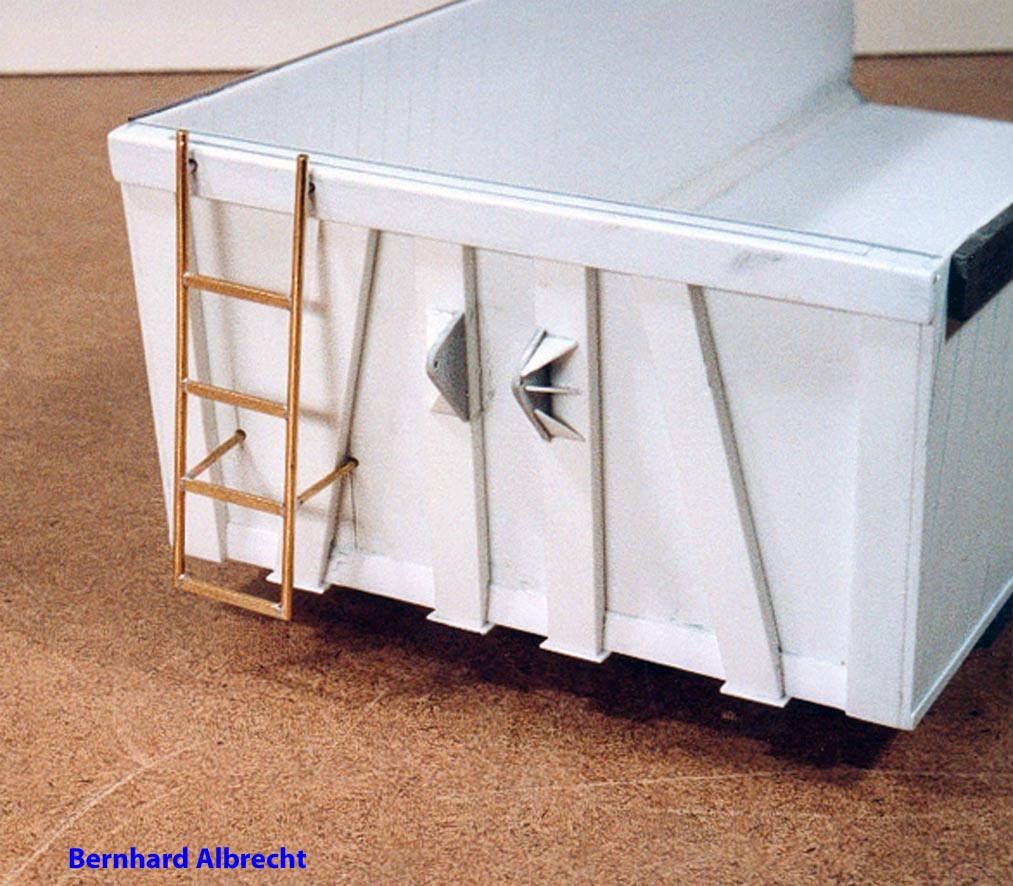 |
Die
Stirnwand entstand ebenfalls aus 1,5mm starkem Polystyrol und wurde so
auf den Boden geklebt, dass sie exakt mit dem Ende des Bodens fluchtet.
Da sich die Stirnwand schräg nach vorne neigt, war es hilfreich, in die
Unterkante der Stirnwand eine leichte Gehrung zu schleifen, um eine
größere Klebefläche zu erhalten. Nun wurden die Seitenteile an den
Muldenboden und die Stirnwand angeklebt, und zwar so, dass die
Seitenteile der Mulde etwas über 3mm über die Stirnwand nach vorne
überstehen. In diese Nische wurde ein Evergreen-Profil 6,3x3,2mm als
Verstärkungsrunge geklebt. Aus dem gleichen Material wurden auch weitere
Streben auf der Stirnwand nachgebildet: Die beiden senkrechten Streben
in der Stirnwandmitte habe ich in einem lichten Abstand von 10mm
voneinander angebracht. Zwischen diese beiden Streben wurde die Konsole
für die Befestigung der Kipppresse montiert. Weitere diagonale Streben
befinden sich rechts und links, jeweils zur Muldenmitte ansteigend. Da
der Bodenrand senkrecht, die Stirnwand aber schräg steht, habe ich die
Streben unteren Bereich etwas angeschliffen, damit sie fluchteten. Auch
der obere Abschluss der Stirnwand wurde mit einer Leiste 6,3x3,2mm
belegt, die ich mit einer weiteren Leiste mit den Maßen 6,3x1,5mm
verstärkt habe. Dies habe ich den Fotos vom Original so entnommen. |
|
|
Komplettiert habe ich die Stirnwand mit einer Leiter, die ich aus 2mm
dickem Messingrohr als Eckstiele und Messingstäben 1,5x1mm als Sprossen
zusammengelötet habe.
In
der Mulde selbst wurden in der Ecke zwischen Boden und Seitenwand
jeweils ein Dreiecksprofil zur Verstärkung eingeklebt. Am Muldenende
habe ich über die unteren Ecken unter Einbeziehung der Dreiecksprofile
ein Knotenblech in Form eines Dreiecks aus 0,75mm Polystyrol geklebt.
Die
Scheuerleiste an der Unterkante der Seitenwände habe ich durch eine
2,5mm breite und 0,4mm dicke Evergreen-Leiste dargestellt.
Nun
musste noch das Lager für die Muldenklappe hergestellt werden. Dazu habe
ich wiederum aus 0,75mm Polystyrol einen 10mm langen Streifen in der
Breite des Obergurts an den Seitenwänden ausgeschnitten und in einem
Abstand von 10mm, gemessen vom Beginn des abgeschrägten Teils der
Seitenwand, als Verstärkung auf den Obergurt geklebt. Die Schrauben-
bzw. Nietköpfe habe ich aus 0,9mm dicken Polystyrolstäben von Evergreen,
die ich in entsprechende Bohrungen eingeklebt habe, dargestellt. In die
Mitte dieser Verstärkungsplättchen habe ich eine Bohrung von 1mm
Durchmesser angebracht, in welcher ein Stück 1mm starker Messingdraht
als Welle eingesteckt werden sollte.
|
|
|
Die
Verschlussklappe der Mulde habe ich wiederum aus 2mm dickem Polystyrol-Material
ausgeschnitten. Diese Klappe bekam die gleichen Verstärkungen ringsum
wie die Oberkante der Muldenwände aus einem 1,5mm dicken und 7,5mm
breiten Streifen Polystyrol. Auch an der Klappe mussten
Verstärkungsplatten in den oberen Ecken (für das Pendellager) sowie an
der Unterkante (für die Verschlüsse) nachgebildet werden. Die Schrauben-
bzw. Nietköpfe habe ich auch an dieser Stelle mit 0,9mm dicken
Polystyrolstäben angedeutet. Auf den Fotos ist eine Art Handgriff an der
Unterkante der Muldenklappe zu sehen. Ich habe
ihn aus 1mm Messingdraht mit den Maßen 13x6mm hergestellt und in zwei
Bohrungen in der Muldenklappe eingesetzt.
Durch die Verwendung des Bodens eines Kofferaufbaus waren schon einige
Längs- und Querstreben vorhanden, die jedoch in Anzahl und Anordnung der
höheren punktuellen Belastung eines Kippaufbaus im Original wohl nicht
ausreichend standgehalten hätten. Deshalb habe ich |
 |
|
|
die Zwischenräume mit weiteren
Querstreben versehen, um dem Vorbildeindruck weiter entgegen zu kommen.
Da ich von den REVELL-Pritsche/Plane Aufbauten für LKW-Oldtimer noch
ziemlich viele Latten aus dem Spriegelgestell übrig hatte, bot es sich
an, diese zu verwenden und als Querverbindungen in den Muldenboden
einzusetzen. Dies ist im Bild anhand der Farbunterschiede der Teile
deutlich zu sehen.
|
|
|
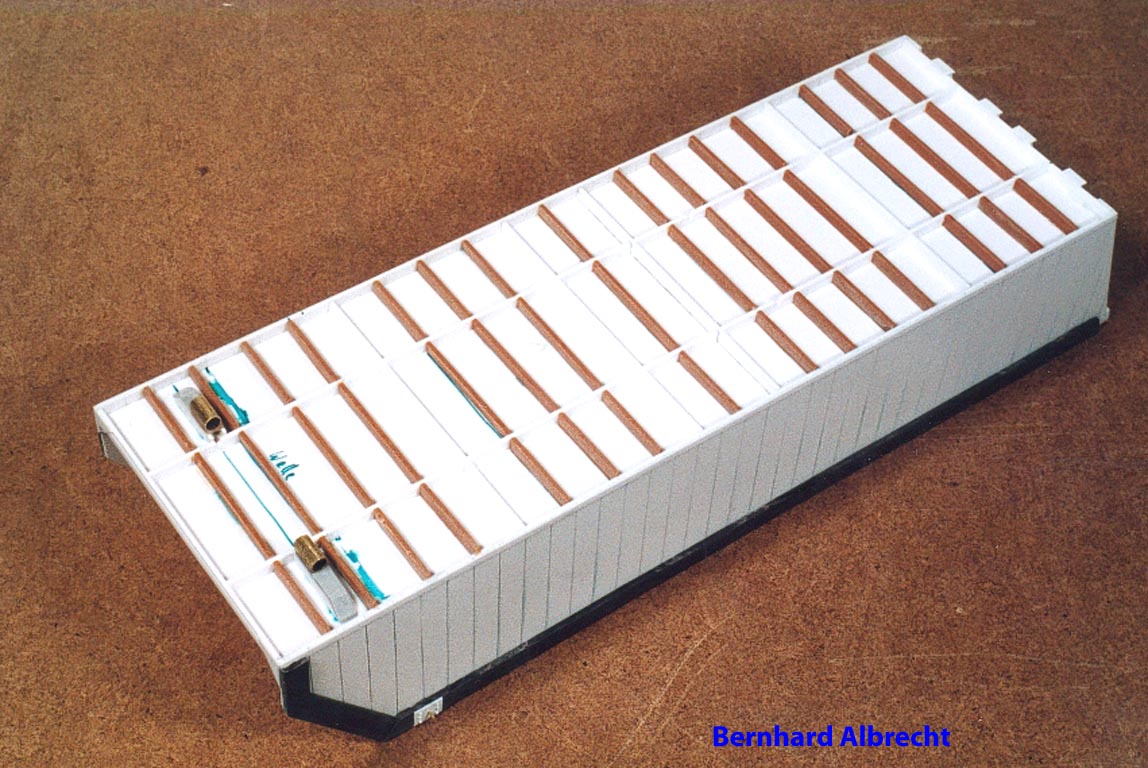 |
Als
Nächstes habe ich das Kipplager an der Muldenunterseite gebaut. 2,3cm
vom hinteren Ende der Mulde habe ich zwei Messingröhrchen mit 5mm
Durchmesser und einer Länge von 10mm auf zwei Konsolen aus U-Profilen
geklebt. Diese beiden Röhrchen haben einen Abstand von 4,7cm voneinander,
damit das Messingröhrchens, welches auf dem Aufliegerrahmen befestigt
ist, genau dazwischen passt. Wenn man also die Kippbrücke auf den Rahmen
setzte, bildeten die Röhrchen auf dem Fahrgestell und die Röhrchen an
der Kippmulde ein durchgehendes Teil, in welches ein weiteres
Messingröhrchen mit geringerem Durchmesser gesteckt werden konnte.
Dadurch bildeten diese Teile zusammen ein Scharnier und fixierten
gleichzeitig die Mulde auf dem Fahrgestell. Hier war auf exakte Montage
der Röhrchen zu achten, damit nach dem Durchstecken der Innenwelle die
Kippmulde absolut gerade zur Fahrrichtung auf dem Fahrgestellrahmen
auflag. Kippversuche zeigten, dass alles zu meiner Zufriedenheit
funktionierte. Für die weitere Bearbeitung und Lackierung habe ich nach
der „Anprobe“ |
|
|
die
Innenwelle wieder aus den Messingröhrchen heraus gezogen und Mulde und
Fahrgestell wieder voneinander getrennt.
Die Mulde sollte wie das Fahrerhaus eine Lackierung in Zementgrau
erhalten. Auch hier wurde nach einer gründlichen Vorbehandlung in
Seifenlauge vorher mit REVELL-Airbrush-Grundierung die Grundlage für den
Decklack geschaffen.
|
|
|
Da
ich die Kippmulde gelegentlich auch im gekippten Zustand zeigen wollte,
habe ich mir eine Presse mit ausgefahrenen Stempeln gebastelt. Ich nahm
dazu drei gleich lange Kunststoffröhrchen, die in ihrem Durchmesser so
beschaffen waren, dass sie jeweils ineinander gesteckt werden konnten.
Diese klebte ich dann zusammen, indem ich jedes Röhrchen ca. 10mm weit
in das nächst größere hinein steckte. Am Ende mit dem dünnsten Röhrchen
bastelte ich eine Gabel als Lager. Mit diesem Lager sollte sich der
Stempel am Aufliegerfahrgestell abstützen. An der gegenüberliegenden
Seite des Stempels montierte ich einen kurzen Rohrstumpf, den ich in die
Presse an der Kippmulde einstecken konnte. Anschließend wurde das Ganze
in der Farbe des Aufliegerrahmens lackiert. Die blanken Teile habe ich
dann mit Bare Metal-Chromfolie bezogen.
Die Aufliegeranschlüsse habe ich mit dünnen Drähten bzw. Litzen aus dem
Modellbahnbedarf hergestellt. Kleinigkeiten davon sind auch im Italeri
Zurüstset enthalten. |
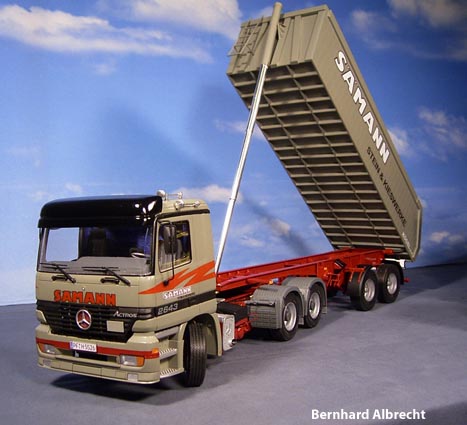 |
|
|
Beschriftung
Die
Beschriftung wurde im Wesentlichen auf Decalfolie für
Tintenstrahldrucker hergestellt. Für den Firmennamen in weißen
Buchstaben mit schwarzem Rand stand mit ein Font mit sehr ähnlichem
Aussehen in meinem PC zur Verfügung. Ich druckte den Schriftzug auf
weiße Decalfolie und schnitt die einzelnen Buchstaben nach der Fixierung
mit Klarlack aus. Alle anderen Schriften erfolgten auf durchsichtiger
Decalfolie. Andere Schriftteile sowie die Nummernschilder wurden
abfotografiert, im PC bearbeitet und entweder auf Decalfolie oder
Fotopapier (Nummernschilder) ausgedruckt und am Modell angebracht.
Ich
hoffe, auch mit diesem Bericht wieder einige brauchbare Anregungen
gegeben zu haben und wünsche viel Spass und Erfolg bei der
Verwirklichung eigener Umbauten.
Modellbauclub WERKSTATT 87
Bernhard Albrecht |
|
|
|
|
|
|
|
|